State-Of-The-Art Motor Technology Helps Your PowerPro® Work Harder For You
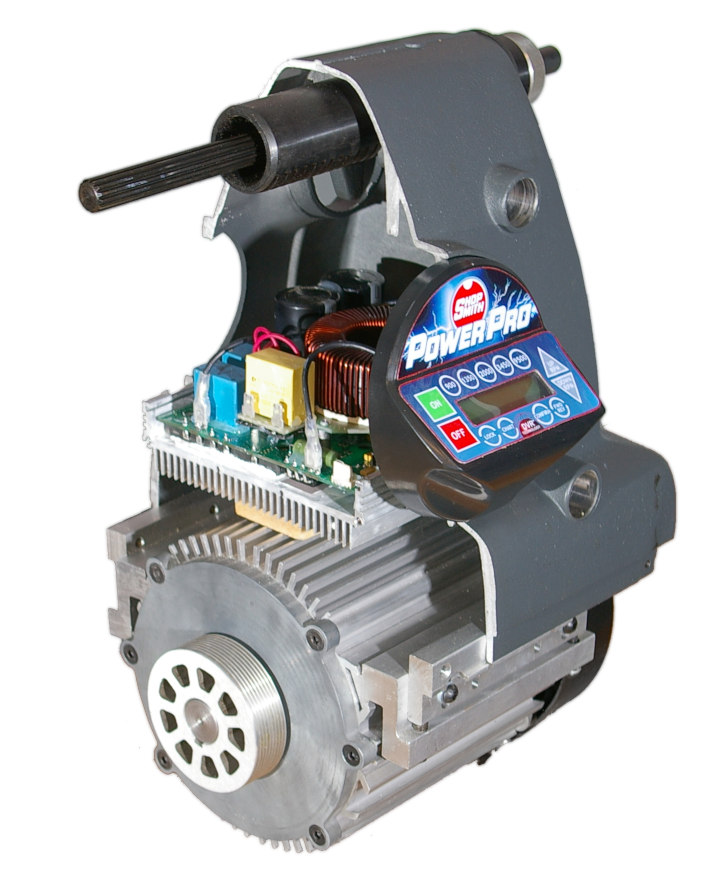
The PowerPro® Smart Motor features a DVR (Digital Variable Reluctance) Motor that is really quite amazing. Unlike dumb AC or DC motors, DVR motors are controlled by a computer that analyzes the spindle position and power needed to maintain a given speed at up to 400 times per second.
Then it uses Power Factor Correction technology to adjust the power delivery eliminating slow-downs, over-revving and losses of power that can negatively affect your project results.
In addition, DVR Motors save energy and emissions over conventional motors and are even smart enough to know whether you’re plugging them into a 120 Volt or 240 Volt outlet without any adjustments beyond switching the plugs on their power cords.

The PowerPro® Motor is a totally enclosed, fan cooled, 35-pound bruiser that’s been scientifically engineered to stand up to all the punishment you can dish out without complaint. It’s encircled by heat dissipating fins and fanned by oversized vanes that keep it cool under even the most taxing conditions.
Working in concert with the Computerized Motor Controller, it will give you 1-3/4 HP when operating at 120 Volts and a full 2HP when operating at 240 Volts and at least TWICE the torque of your current MARK V motor throughout its full speed range.

Computerized Motor Controller makes it all possible The PowerPro® Motor Controller maintains a constant watch over every operation. The 6″ x 6-1/2″ covered Controller fits snugly above the Motor and is, in effect, a highly sophisticated Computer that constantly monitors the performance of your PowerPro® to maintain the selected speed regardless of the load, while optimizing the Motor’s power consumption.
Countless hours of in-shop testing and re-testing ensured proven performance During the developmental stages, every operational aspect of the PowerPro® was tested and re-tested to be certain that it would perform to our highest expectations – and yours, of course!

The most notable of these tests involved a punishing trial of the machine’s ability to keep performing during a grueling thickness planing study. We started with a sizable stack of 8-foot long by 2″ thick by 6″ to 8″ wide white oak boards.
We set our MARK V-powered Shopsmith Thickness planer for the fastest feed rate and a 3/64″ depth-of-cut, then started feeding our boards through the planer. We continued this process over several weeks in one-hour increments without stopping until we had fed a mile of white oak through our planer with no bogging, no complaining and no overheating !